"Living Lab" - Virtuelle Fabrik
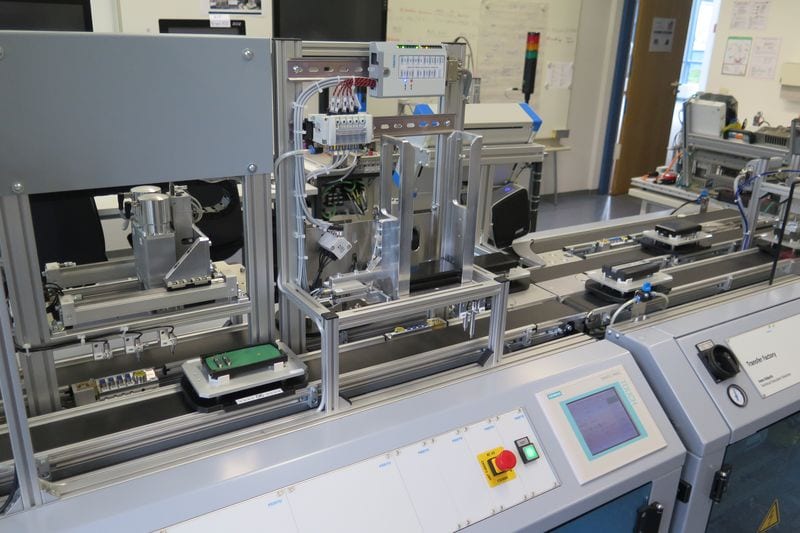
Der Begriff ,"Industrie 4.0" steht für die vierte industrielle Revolution, einer neuen Stufe der Organisation und Steuerung der gesamten Wertschöpfungsketten entlang des Lebenszyklus von Produkten. Dieser Zyklus orientiert sich an den zunehmend individualisierten Kundenwünschen und erstreckt sich von der Idee über die Entwicklung und Fertigung, die Auslieferung eines Produktes an den Endkunden bis hin zum Recycling. Er umfasst auch die damit verbundenen Dienstleistungen (www.plattform-i40.de).
Basis ist die Verfügbarkeit aller relevanten Informationen in Echtzeit durch Vernetzung der an der Wertschöpfung beteiligten Instanzen sowie die Fähigkeit, aus den Daten den zu jedem Zeitpunkt optimalen Wertschöpfungsfluss abzuleiten. Durch die Verbindung von Menschen, Objekten, Produkten und Systemen entstehen dynamische, echtzeitoptimierte und sich selbst organisierende, unternehmensübergreifende Wertschöpfungsnetzwerke. Die Konzepte und Technologien einer "Industrie 4.0" erfüllen die Anforderungen der Industrieunternehmen - insbesondere im Maschinen- und Anlagenbau - und ermöglichen so beispielsweise die Fertigung kundenindividueller Produkte zu Kosten, Ressourceneinsatz und Lieferzeiten von Serien- und Massenprodukten.
"Living Lab" - Virtuelle Fabrik
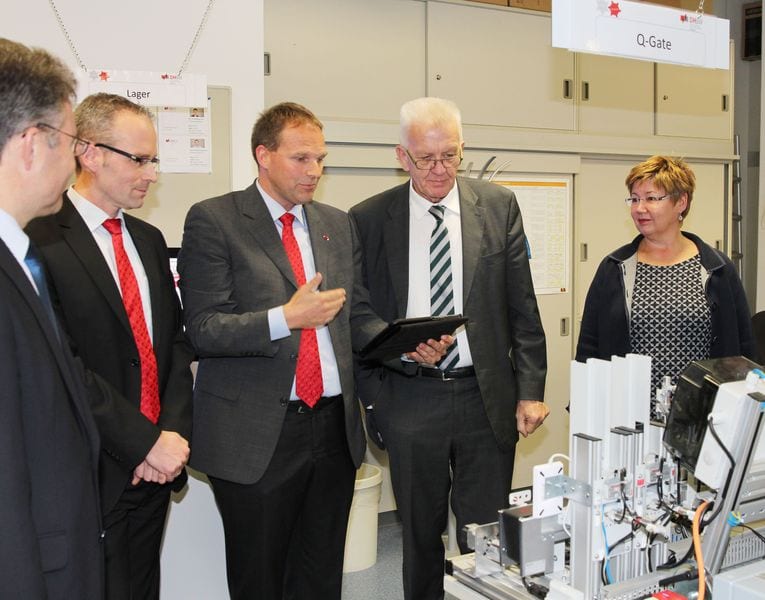
In Zusammenarbeit mit verschiedenen Dualen Partnern wird der Aufbau einer Modellfabrik mit realitätsnah simulierten Prozessen in Produktion, Logistik, Service und Anlagenmanagement durchgeführt. Diese soll nicht nur aufgebaut und dann in Lehre, Forschung und Transfer genutzt werden sondern "leben", d.h. stetig verändert, angepasst und erweitert werden ("Living Lab"). Hiermit wird die Umsetzung von Innovationen im Umfeld der "Produktion der Zukunft" zielgerichtet gefördert und in die betriebliche Praxis transferiert.
Typische Produktionsanlagen und Fertigungsprozesse, insbesondere auch von mittelständischen Betrieben (KMUs), können dort in Form von Modellen mit realen industriellen Komponenten, verteilter Automatisierungstechnik sowie echtzeitfähigen Simulationssystemen abgebildet und mit realen Informationssystemen (ERP, MES, SCADA,...) vernetzt, analysiert und gesteuert werden. Ein zukunftsfähiges Kennzahlenmanagement und ein Ausnahmeprozess auf Grundlagen einer echtzeit- und massendatenfähigen Prozessdatenarchitektur (OPC, Hadoop-Cluster) sind wichtige Pfeiler der Gesamtlösung. Des Weiteren sind Methoden und Komponenten zur automatischen Identifikation von Objekten (1D/2D-Barcodes, RFID,NFC) bis hin zum Digitalen Produktgedächtnis ebenso Teil des Labors wie auch aktuelle Konzepte zur Mensch-Maschine-Interaktion inklusive Web-Schnittstellen und mobile Lösungen zur Visualisierung und Steuerung über eigenentwickelte Apps.
Die ,,Digitale Fabrik" des Kompetenzzentrums ,,Fertigungs- und Informationsmanagement" der DHBW Mosbach ist als einer von ,,100 Orten für Industrie 4.0" in Baden-Württemberg ausgezeichnet worden. Damit ist die DHBW Mosbach die erste und bisher einzige Hochschule, die diese Auszeichnung erhalten hat.
Ausbildung und Forschung
Dieser interdisziplinäre Ansatz ermöglicht eine umfassende, bedarfsgerechte und praxisorientierte Ausbildung der zukünftigen Ingenieure in den Studiengängen Wirtschaftsingenieurwesen, Elektrotechnik, Maschinenbau und Mechatronik, aber auch der Informatik und Wirtschaftsinformatik.
Mit "E-FIT" (,Evolutionäre Fertigungs-IT´) wurde zudem ein erstes Forschungsprojekt gestartet, um Mensch, Maschine und IT-Systeme in der Produktion informationstechnisch zu vernetzen. Im Rahmen des Projektes wird untersucht, wie innovative Produktions- und Logistikprozesse zusammen mit moderner Informations- und Kommunikationstechnologie einen entscheidenden Mehrwert und Effizienzgewinn für Unternehmen ermöglichen. Hierunter fällt auch die Analyse neuer Geschäftsmodelle auf Basis der erweiterten Möglichkeiten.
Folgende Studiengänge nutzen das Labor:
Angewandte Informatik
Elektrotechnik
Maschinenbau - Konstruktion und Entwicklung
Maschinenbau - Kunststofftechnik
Maschinenbau - Verfahrenstechnik
Maschinenbau - Virtual Engineering
Mechatronik
Wirtschaftsinformatik
Wirtschaftsingenieurwesen - Innovations- und Produktmanagement
Wirtschaftsingenieurwesen - Internationale Produktion und Logistik
Wirtschaftsingenieurwesen - Internationales Technisches Projektmanagement
Wirtschaftsingenieurwesen - Internationales Technisches Vertriebsmanagement
Kontakt
- Studiengangsleitung Elektrotechnik und Informationstechnik
- Sprecher des Kompetenzzentrums Fertigungs- und Informationsmanagement
- Telefon
- 06261 939-540